Specialist Recommendations on What is Porosity in Welding and Exactly How to Address It
Unraveling the Secret of Porosity in Welding: Tips for Decreasing Issues and Making The Most Of Quality
In the detailed world of welding, porosity remains a relentless difficulty that can considerably influence the top quality and stability of welded joints. As we dig into the depths of porosity in welding, discovering the tricks to its avoidance and control will be vital for experts seeking to master the art of top notch weldments.
Understanding Porosity in Welding
Porosity in welding, a common concern come across by welders, refers to the visibility of gas pockets or spaces in the welded material, which can compromise the integrity and high quality of the weld. These gas pockets are commonly entraped throughout the welding process because of different factors such as inappropriate securing gas, polluted base materials, or incorrect welding parameters. The development of porosity can weaken the weld, making it susceptible to splitting and corrosion, inevitably causing structural failings.
Recognizing the root causes of porosity is crucial for welders to successfully prevent its occurrence. By identifying the significance of maintaining proper gas protecting, guaranteeing the sanitation of base products, and maximizing welding setups, welders can considerably minimize the likelihood of porosity development. Additionally, using methods like preheating the base product, utilizing correct welding techniques, and carrying out complete inspections post-welding can further help in reducing porosity flaws. On the whole, a thorough understanding of porosity in welding is important for welders to create top notch and sturdy welds.

Common Causes of Porosity
When evaluating welding processes for potential quality problems, comprehending the typical reasons of porosity is crucial for maintaining weld integrity and preventing structural failings. Porosity, identified by the existence of dental caries or gaps in the weld metal, can dramatically endanger the mechanical properties of a welded joint.
In addition, welding at inappropriate criteria, such as excessively high travel rates or currents, can produce extreme turbulence in the weld pool, trapping gases and creating porosity. By dealing with these usual causes via appropriate gas protecting, product prep work, and adherence to optimum welding specifications, welders can decrease porosity and improve the top quality of their welds.
Methods for Porosity Avoidance
Implementing efficient preventive steps is important in minimizing the incident of porosity in welding procedures. One strategy for porosity prevention is ensuring correct cleaning of the base metal prior to welding. Impurities such as oil, oil, corrosion, and paint can lead to porosity, so detailed cleansing using proper solvents or mechanical approaches is crucial.

Making use of high-quality filler products and securing gases that are appropriate for the base steel and welding process can considerably minimize the risk of porosity. In addition, maintaining appropriate welding parameters, such as voltage, existing, travel rate, and gas circulation price, is essential for porosity avoidance.
Moreover, employing proper welding techniques, such as preserving a consistent traveling rate, electrode angle, and arc length, can aid prevent porosity (What is Porosity). Sufficient training of welders to guarantee they adhere this hyperlink to ideal practices and top quality control procedures is additionally important in lessening porosity flaws in welding
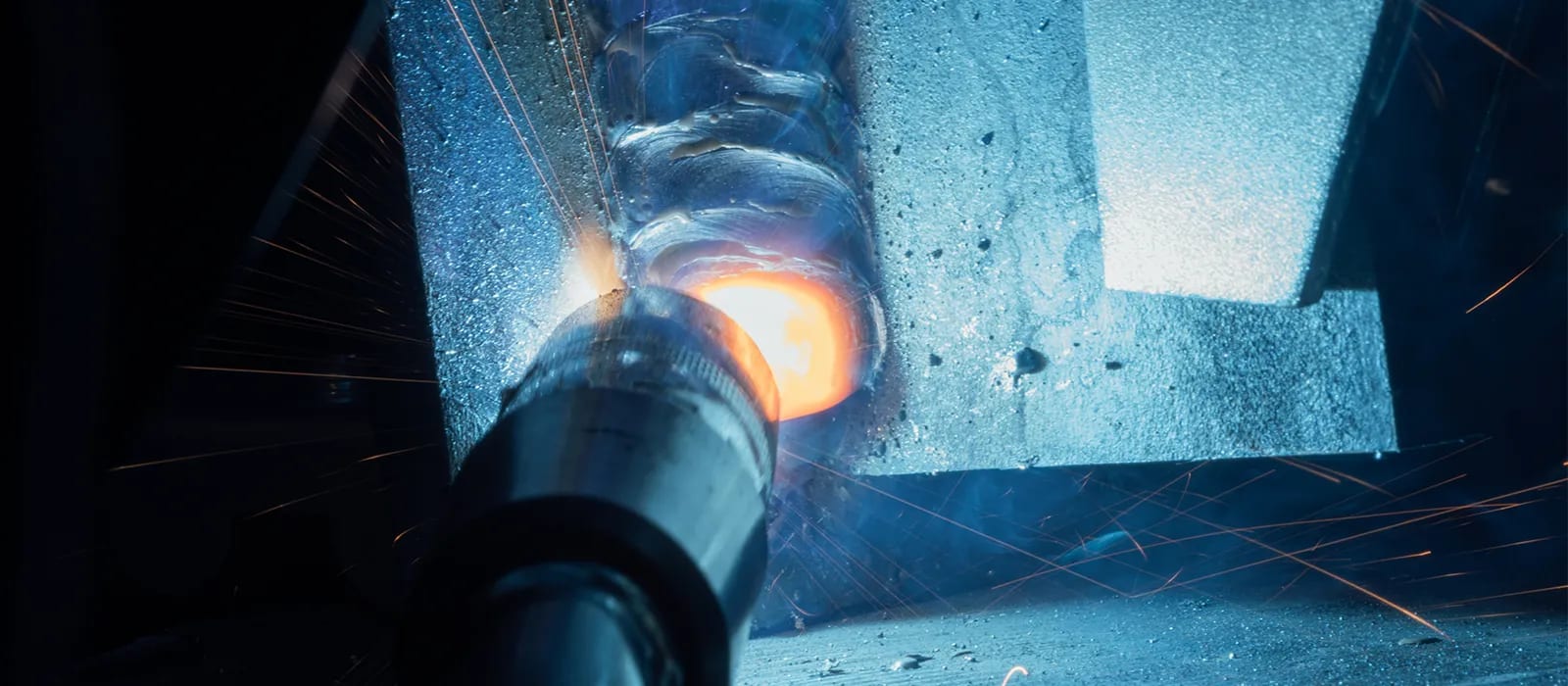
Finest Practices for Quality Welds
One key technique is maintaining correct cleanliness in the welding area. Completely cleaning up the workpiece and bordering area prior to welding can aid minimize these concerns.
One more best practice is to thoroughly choose the proper welding criteria for the particular materials being joined. This includes establishing the correct voltage, present, take a trip rate, and securing gas flow price. Proper specification option makes sure optimal weld penetration, blend, and total quality. Moreover, making use of high-grade welding consumables, such as electrodes and filler steels, can substantially affect the final weld quality. Investing in costs consumables can result in more powerful, much more resilient welds with less defects. By adhering to these best practices, welders can constantly generate high-quality welds navigate here that fulfill industry standards and exceed consumer assumptions.
Significance of Porosity Control
Porosity control plays a vital function in guaranteeing the great post to read honesty and quality of welding joints. Porosity, characterized by the existence of dental caries or spaces within the weld steel, can dramatically endanger the mechanical properties and architectural integrity of the weld. Too much porosity weakens the weld, making it much more at risk to cracking, rust, and total failure under operational loads.
Effective porosity control is crucial for keeping the wanted mechanical homes, such as stamina, ductility, and durability, of the bonded joint. What is Porosity. By decreasing porosity, welders can boost the total top quality and reliability of the weld, guaranteeing that it fulfills the efficiency requirements of the desired application
Additionally, porosity control is vital for attaining the desired aesthetic look of the weld. Too much porosity not just compromises the weld however also diminishes its visual charm, which can be critical in industries where aesthetics are necessary. Correct porosity control techniques, such as using the proper securing gas, managing the welding specifications, and guaranteeing appropriate sanitation of the base products, are crucial for creating high-grade welds with very little flaws.
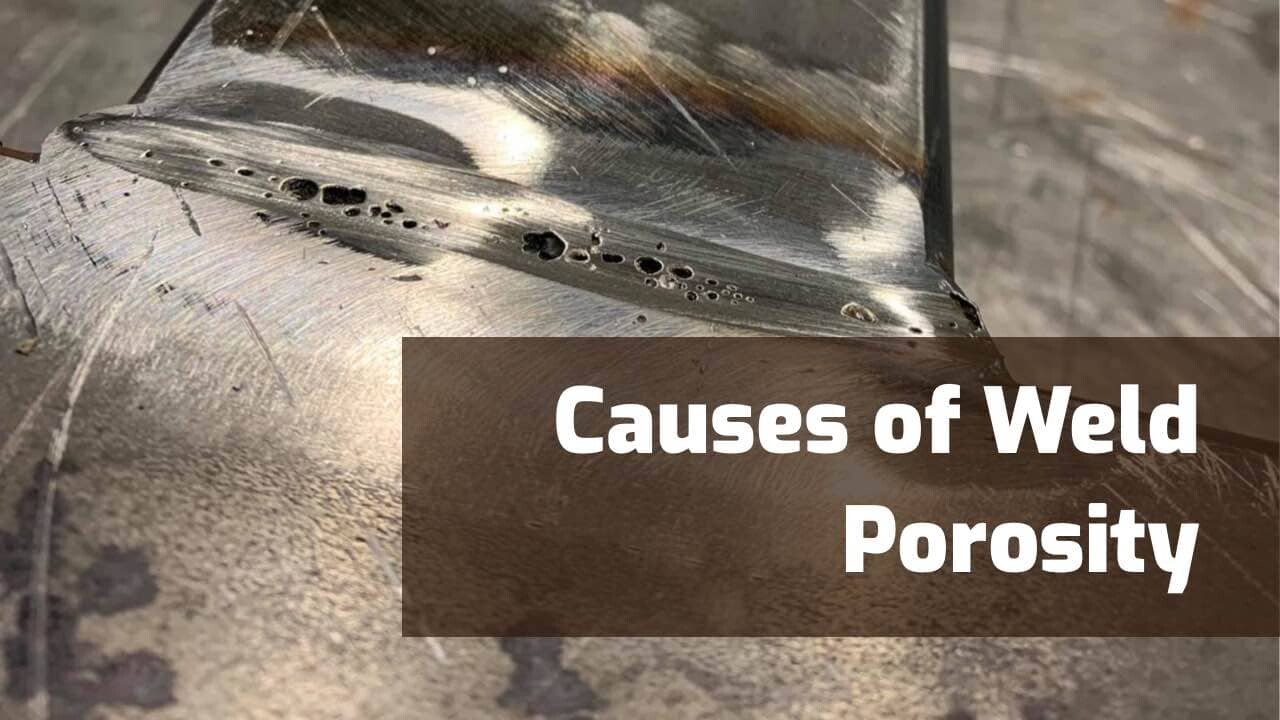
Conclusion
In conclusion, porosity in welding is an usual issue that can endanger the quality of the weld. It is important to regulate porosity in welding to guarantee the stability and toughness of the final item.